Розрізняють два види добавок: - тонкомелені,; які, вводять, у кількості 5...20,% до маси цементу для його економії й одержання щільного та стійкого бетону при малих витратах цементу, і хімічні, які вводять у невеликій кількості (0,1...2,0 % до маси цементу) для змінювання властивостей бетонної суміші та бетону в потрібному напрямі. За тонкомелені добавки беруть золу - винос теплових електростанцій, одержувану як високодисперсні відходи від спалювання вугілля, мелені шлаки тощо. Проте все більшого поширення набувають численні хімічні добавки, які класифікуються за функціональним призначенням та основним ефектом дії. Пластифікуючи добавки збільшують рухливість, тобто знижують жорсткість суміші, не знижуючи міцності, бетону. Як пластифікатори широко використовують поверхнево-активні речовини (ПАР), часто одержувані з вторинних продуктів та відходів хімічної промисловості. За характером дії розрізняють гідрофільно та гідрофобно-пластифікуючі добавки. Представником гідрофільно-пластифікуючих добавок є ЛСТ (лігносульфонат технічний, колишня назва СДБ — сульфатно-дріжджева бражка). Як у рідкому, так і в твердому вигляді легко розчиняється у воді. До гідрофобно-пластифікуючих добавок належать милонафт, гід-рофобізуючі сполуки ГКЖ-10 (етилсиліконат натрію), ГКЖ-11 (метилсиліконат натрію), ГКЖ-94 (етилгідросилоксанова рідина). Прискорювачі твердіння призначаються насамперед для наближення строків розпалублення при монолітному бетонуванні, а у виробництві збірного залізобетону — для скорочення режимів теплової обробки виробів та збільшення оборотності борт-оснащення. Найпоширенішими в практиці прискорювачами є: хлорид кальцію СаСl2, сульфат натрію Na2SО4, поташ К2СО3, нітрати кальцію Са(NO3)2 та натрію NaNО3. Дія цих прискорювачів полягає в тому, що вони знижують розчинність гідроксиду кальцію Са(ОН)2, який утворюється при гідратації цементу. Цим стимулюється подальша гідратація клінкерних мінералів і збільшується кількість новоутворень, що зумовлює підвищене зростання міцності в перші 3...7 діб.[11] Іноді застосовують і комбіновані добавки, наприклад нітрит-нітрат кальцію, нітрит-нітрат-хлорид кальцію. Щоб сповільнити тужавіння цементу, застосовують добавки, які одночасно зменшують водопотребу суміші та витрату цементу. Суміші на основі вапняних в'яжучих. Сировиною для виготовлення цих матеріалів і виробів є будівельне вапно чи в'яжучі, які містять його, а також заповнювачі, що містять кремнезем. Виробництво їх ґрунтується на гідротермальному синтезі гідросилікатів кальцію, здійснюваному в автоклаві при підвищених значеннях тиску й температури водяної пари. Тому такі матеріали й вироби дістали назву автоклавних силікатних. Як в’яжуче для автоклавних силікатних матеріалів звичайно використовують повітряне кальцієве негашене вапно, яке містить не менш як 70% активних СаО+МgО і не більш як 5% МgО. Аби підвищити міцність готових виробів, замість вапна застосовують вапняно-піщане в'яжуче, виготовлене одночасним помелом грудкового негашеного вапна та кварцового піску. Змінюючи співвідношення між Як заповнювачі автоклавних силікатних матеріалів найчастіше використовують кварцові піски. Можна застосовувати також польовошпатні та карбонатні піски, проте фізико-механічні властивості виробів при цьому погіршуються. Значно рідше застосовують гравійно-піщані суміші, а також пористі заповнювачі (керамзит, аглопорит, шлакову пемзу, спучений перліт тощо). Вода для виробництва матеріалів та виробів на вапняних в'яжучих має задовольняти ті самі вимоги, що й при виробництві бетонних виробів на основі цементних в'яжучих. Добавки, застосовувані у виробництві автоклавних силікатних матеріалів та виробів, призначаються для регулювання властивостей формувальних сумішей та готової продукції. Це .можуть бути ущільнювальні (тонкодисперсні мінеральні порошки), укрупнювальні (крупніші за зерновим складом заповнювачі), пластифікуючі, пороутворювальні добавки, а також пігменти, що надають виробам забарвлення й декоративних властивостей. Суміші на основі гіпсових в'яжучих. Для виготовлення зазначених вище сумішей залежно від їх призначення використовують повітряні низько- та високовипалювані гіпсові в'яжучі, а також гідравлічні гіпсоцементнопуцоланові в'яжучі. Як важкі заповнювачі застосовують природні гравій та пісок, а як легкі — щебінь з вапняку-черепашнику, вулканічного туфу, вулканічної пемзи, керамзит, аглопорит, шлакову пемзу, спучений перліт, доменні та паливні шлаки й золи, а також органічні заповнювачі — деревну стружку й тирсу, солому, очеретяну січку, лляну кострицю, паперову макулатуру тощо. Заповнювачі поліпшують пластичні властивості формувальних сумішей, зменшують питому витрату в'яжучого, знижують формувальну вологість суміші та усадку. Щоб мати задані технічні та фізико-хімічні властивості формувальних сумішей та готових виробів, до гіпсових композицій уводять добавки, які можна поділити на дві групи. Добавки першої групи регулюють строки твердіння й пластичність формувальних сумішей, добавки другої групи змінюють властивості затверділих виробів. Як добавки першої групи звичайно застосовують: тваринний клей, ЛСТ, вапно, лимонну кислоту та її солі— для сповільнення строків тужавіння в'яжучих; кухонну сіль, сульфат натрію, двоводяний гіпс — для прискорення строків тужавіння.[12] Найважливішими добавками другої групи є пороутворювачі, гідрофобізатори, гідравлічні добавки тощо. Пороутворювальні добавки, застосовувані для виготовлення високопористих виробів, поділяють на газоутворювачі (їдкий натр, пероксид водню, розведена сірчана кислота, вуглекальцієві солі) та піноутворювачі (клеєканіфольний, смолосапоніновий). Мастики Мастика — це суміш нафтового бітуму чи дьогтю (відігнаного й складеного) з мінеральним наповнювачем, емульгатором та добавкою антисептика. Для приготування мастик використовують: пилуваті наповнювачі—тальк, магнезит, вапняк, доломіт, крейду, цемент, золу; волокнисті заповнювачі — азбест, мінеральну вату тощо. До бітумних матеріалів належать природні бітуми, асфальтові породи, нафтові бітуми. Природні бітуми — це в'язкі рідини та твердоподібні речовини. Природні бітуми утворилися внаслідок природного процесу окислювальної полімеризації нафти. Вони зустрічаються в місцях нафтових родовищ, утворюючи лінзи, а іноді й асфальтові озера. Проте природні бітуми в чистому вигляді зустрічаються рідко, найчастіше вони містяться в осадових гірських породах. Асфальтові породи — це пористі гірські породи (вапняки, доломіти, піщаники, глини, піски,, сланці), просочені бітумом; Із цих порід виділяють бітум або їх розмелюють і застосовують у вигляді асфальтового порошку. Нафтові (штучні) бітуми, здобуті переробкою нафтової сировини, залежно від технології виробництва можуть бути: залишковими, одержуваними з гудрону за допомогою подальшого глибокого відбирання з нього масел; окислені, одержувані окисленням гудрону в спеціальних апаратах (продуванням повітря), крекінгові, одержувані переробкою залишків, утворюваних при .крекінгу нафти. Гудрон — це залишок відгонки з мазуту масляних фракцій; він-є основною сировиною для одержання нафтових бітумів (використовують його як зв'язуючу речовину в дорожньому будівництві). До дьогтьових матеріалів належать сирий .кам'яновугільний відігнаний дьоготь, пек, складений дьоготь Фарбові суміші. Зв'язуючі речовини: Призначення зв'язуючих речовин полягає в скріпленні часточок пігменту й наповнювача із зафарбовуваною поверхнею. Зв'язуючими речовинами у фарбових сумішах є такі матеріали: полімери — у полімерних фарбах, лаках, емалях; каучук — в каучукових фарбах; оліфи — в олійних фарбах; клеї (тваринний і казеїновий) — у клейових фарбах; похідні целюлози — у нітролаках; неорганічні в'яжучі речовини — у цементних, вапняних, силікатних фарбах. Полімери застосовують у фарбах і лаках разом із: розчинником, а також у поєднанні з-оліфою чил цементом1 (полімерцементні фарбові суміші). Використання синтетичних полімерів ; значно скорочує витрату рослинних олій на виробництво фарбових сумішей, розширює асортимент довговічних та економічних фарбових сумішей нових видів.[13] Зв'язуюче вибирають з урахуванням міцності його зчеплення з основою (адгезії) після затвердіння. Для безводних сумішей зв'язуючими є оліфи та синтетичні водонерозчинні полімери, що забезпечують водостійке покриття, як цементи та рідке скло. Пігменти: пігментами називають тонкодисперсні порошки, нерозчинні у зв'язуючій речовині й розчиннику і здатні в суміші з ним утворювати непрозорі покриття різних кольорів і відтінків. Вибір того чи: іншого пігменту й фарбового складу зумовлюється насамперед призначенням фарбованого покриття та вартістю фарбової речовини. Білі пігменти. Крейду як пігмент і наповнювач використовують для розбілювання кольорових фарбових речовин. її застосовують також для виготовлення клейових та силікатних фарб. Для олійних фарб крейду не використовують, оскільки в суміші з оліфою утворюються плівки з жовтим відтінком. Вапно повітряне застосовується Для того, Щоб білити фасади промислових га громадських споруд. Серед штучних білих пігментів, одержуваних хімічною переробкою мінеральної сировини, найчастіше використовують цинкові, свинцеві, титанові білила та літопон (сірчисті білила). Чорні пігменти. Сажі мають високу барвну здатність, покривність і стійкість щодо дії лугів та кислот. Діоксид марганцю МgО2 у тонкодисперсному стані має хорошу покривну здатність. Його здобувають із природної марганцевої руди. Графіт — це пігмент сірувато-чорного кольору; за хімічним складом має високий вміст вуглецю (до 95%). Використовується для виготовлення олійних фарбових сумішей, має стійкість до дії кислот та високих температур. Червоні пігменти. Залізний сурик випускають у вигляді тонкого порошку оксиду заліза цегляно-червоного кольору або інших відтінків, залежно від співвідношення складових частин Рb2О3 і СаSО4. Свинцевий сурик — порошок червоно-оранжевого кольору, який містить в основному РbО та Рb2О3. Токсичний і досить важкий пігмент (істинна густина 8,32...9,16 г/см3), застосовується в антикорозійних олійних фарбових сумішах по металу та дереву. Крон червоний має високу світлостійкість та здатність захищати Сталеві конструкції від корозії. За хімічним складом це хромовокислий свинець. Редоксайд — червоний залізоокисний пігмент, який має підвищену стійкість до дії лужного середовища. Використовують для фарбування по деревині та штукатурці. Жовті пігменти. Крон свинцевий — штучний пігмент, одержуваний внаслідок хімічної взаємодії хромпику із солями свинцю, має колір від світло-лимонного до темно-жовтого, токсичний. Завдяки високій покривній здатності та антикорозійній стійкості крон широко використовується в лакових і олійних фарбових сумішах по металу та дереву. Покривність крону 40...190 г/м2, істинна густина 6,12 г/см3. Вохри — природні пігменти жовтого, коричневого та червоного кольорів. їх здобувають із глин, які містять до 25 % (за масою) Ре2О3. Колір вохри залежить від вмісту оксиду заліза. Це найдешевші пігменти, їх широко застосовують для виготовлення фарб.[14] Сині пігменти. Ультрамарин — порошок синього кольору. За хімічним складом це алюмосилікат натрію, який містить сірку в колоїдному стані. Його одержують випалюванням композицій каоліну із содою та сіркою або сірчанокислого натрію з вугіллям. Значного поширення ультрамарин набув як барвник в олійних сумішах з метою усунення жовтих відтінків. Лазур — інтенсивний штучний пігмент темно-синього кольору. Це порошок залізної солі залізисто-синеродистої кислоти. Світлостійкий пігмент, проте руйнується під дією лугів і тому не застосовується для фарб по штукатурці та цементних розчинах. Зелені пігменти. Оксид хрому Сr2О3 стійкий до дії лугів, кислот та підвищених температур. Щоб одержати зеленкувато-сині відтінки, добавляють ультрамарин. Цинкову зелень одержують, змішуючи крони, малярну лазур та наповнювач ВаSО4. Її використовують у фарбових сумішах для робіт по металу та дереву. Зелень свинцева хромова — це механічна суміш жовтого крону з лазур'ю та наповнювачем. За властивостями подібна до жовтого свинцевого крону: має високу покривність, барвну здатність та антикорозійні властивості. її використовують в олійних фарбових сумішах, проте внаслідок руйнування пігменту в лужному середовищі вона не придатна для робіт по штукатурці та цементних розчинах. Металеві порошки застосовують у фарбових сумішах для декоративних робіт по металу. Пудра алюмінієва — це тонкодисперсний, лускатоподібний порошок сріблястого кольору, добре відбиває сонячне проміння. Покривність її ,10 г/м2, істинна густина 2,5...2,6 г/см3. Пудру добавляють до лаку перед його використанням, аби надати йому антикорозійних властивостей.[15] 1.2.2. Технологія виробництва Технологія виробництва будівельних сумішей в загальному випадку полягає у змішуванні відповідних компонентів суміші. Проте для кожного виду суміші вона відрізняється. Наприклад з метою досягнення потрібних кінцевих результатів раціональна й економічна технологія висуває до всіх бетонних сумішей наступні вимоги. До закінчення формування суміші мають перемішуватися, транспортуватися й укладатися з найменшими затратами енергії; не розшаровуватися; швидкість твердіння відформованого бетону має відповідати заданим строкам розпалублення; витрата цементу в суміші має бути обґрунтовано мінімальною, оскільки він є найдорожчим компонентом.[16] Щоб можна було готувати шлаколужні бетонні суміші, бетонозмішувальні вузли та заводи залізобетонних виробів потрібно дообладнати технологічною лінією приготування розчину лужного компонента. Суміші рекомендується готувати в бетонозмішувачах примусової дії, бетонні суміші на крупному заповнювачі — в бетонозмішувачах гравітаційної дії. Тривалість перемішування шлаколужних бетонних сумішей, як правило, не відрізняється від тривалості перемішування сумішей на портландцементі. Якщо треба подовжити строки збереження легкоукладальності, то розчин лужного компонента вводять у два прийоми з інтервалом 2...3 хв. Неприпустимо змішувати шлаколужні бетонні суміші з сумішами на інших видах в’яжучих Виробничі приміщення та лабораторії, де проводять роботи з лужним компонентом, мають бути обладнані припливио-витяжною механічною вентиляцією, яка забезпечує допустиму концентрацію пилу в повітрі робочої зони в перерахунку на NaOH не більш як 0,5 мг/м3. Шлаколужні бетонні суміші можуть використовуватися в умовах від'ємних температур. Для бетонів, які тверднуть в умовах від'ємних температур (до —15 °С), слід застосовувати швидкотверднучі шлаколужні в'яжучі, в яких лужними компонентами є рідкі луги чи метасилікат натрію. Головну роль у змінюванні стану суміші відіграє цементне тісто, а в ньому — властивості в'яжучого. Структурна в'язкість цементного тіста залежить від концентрації твердої фази у водній суспензії. У процесі випробування цементу це виражається показником нормальної густоти тіста (НГ) — умовним ступенем пластичності, потрібним для наступних випробувань, а в технології бетону — відношенням В/Ц. Тут корисно простежити: якщо для гідратації цементу стехіометрично потрібно 15...20 % води за масою залежно від мінералогічного складу й тонкості помелу, для нормальної густоти треба — 24...30 %, ю для бетонної суміші —практично 40...70 % (В/Ц = 0,4...0,7). Потреба щодо надлишків води диктується лише реологічними умовами перемішування та ущільнення. Під час бетонування для забезпечення потрібної якості бетону після його затвердіння бетонна суміш повинна мати консистенцію, яка відповідає умовам її укладання. Мірою консистенції є так звана легкоукладальність — здатність бетонної суміші заповнювати форму чи опалубку з найменшими затратами зовнішньої енергії. Це найважливіший технологічний показник. Щоб оцінити легкоукладальність суміші, розроблено технічні характеристики: рухливість і жорсткість. Рухливість суміші виражають у сантиметрах осадки суміші, яку визначають за допомогою стандартного конуса. Якщо суміш після зняття стандартного конуса не осідає, тобто якщо, то використовують спеціальний прилад для визначення жорсткості в секундах. Для формування жорстких сумішей потрібна механічна дія, наприклад вібрування з привантаженням чи вібропрокатуванням, які можливі лише в умовах заводів залізобетонних виробів. Водночас, використовуючи жорсткі суміші, можна знижувати витрату цементу. Проектування складу бетонної суміші для конкретних умов включає в себе кілька послідовних етапів. 1. Визначення проектних даних: Rб — задана марка бетону за міцністю на стиск, МПа чи кгс/см2; П (ОК.) або Ж — відповідно рухливість (осадка конуса), см, і .жорсткість, с, які характеризують легкоукладальність бетонної суміші. Ці дані беруть з проектної документації. 2. Визначення вихідних даних (характеристики компонентів), вид. цементу, його активність Rц, МПа чи кгс/см2; істинна густина складових (цемент, пісок, щебінь або гравій) — ρц, ρп, ρщ(г), кг/м3; міжзернова пустотність, (об'єм пустот) крупного заповнювача Vп.щ(г), частки одиниці; найменша Dнм та найбільша Dнб крупність зерен заповнювача, мм; насипна густина складових ρц, ρп, ρн.щ(г), кг/м3; вологість заповнювачів, якщо треба виконати перерахунок лабораторного складу бетону на виробничий; якісна характеристика заповнювачів (вміст різних домішок).[17] Зерновий (гранулометричний) склад піску має велике значення для виготовлення бетонної суміші із заданими властивостями. Він характеризується процентним вмістом зерен різних розмірів і так званим модулем крупность Мк. Щоб визначити ці показники, використовують ситовий аналіз. Стандартний набір сит включає в себе послідовно (згори вниз) розміщені сита з вічками: 5; 2,5; 1,25; 0,63; 0,315; 0,16 мм. Залишки піску на кожному ситі зважують і підраховують так звані часткові залишки на кожному ситі, %: 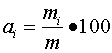 де mi, m — маси відповідно залишку на даному ситі та просіюваної наважки, г. Часткові залишки характеризують розподіл зерен за ступенем крупності в пробі піску. Далі визначають повні залишки з точністю до 0,1 % на кожному ситі як суму часткового залишку на даному ситі і суми залишків на попередніх ситах, %: Ai=a2,5+…+ai де a2,5 +…+ аі — часткові залишки, починаючи з розміру 2,5 мм і включаючи частковий залишок на даному ситі аі, %. Загальну оцінку крупності піску даної проби виражають модулем-крупності:  Проте й при наявності обчислених значень ще не створюється1 достатнє уявлення про ступінь придатності піску за зерновим складом, оскільки не ясно, наскільки компактно поєднуються в піску його1 окремі фракції, зафіксовані ситами. Саме оптимальне поєднання фракцій, забезпечує сипкому матеріалу найменшу міжзернову пустотність, тобто мінімальний об'єм, який має бути зайнятий цементним тістом.. Кінцевий результат полягатиме не лише в економічності бетону (за витратою цементу), а й у поліпшенні деяких його важливих технічних властивостей—зменшенні усадки й повзучості. Для виробництва щебеню подрібнюють вивержені породи — граніт, діабаз, діорит; щільні осадові породи — вапняк, доломіт; метаморфічні кварцити. При* дрібненні на; сучасних кар'єрах його поділяють на фракції: 5...10 мм, 10...20, 20...40, 40...70 мм. У разі потреби (на замовлення споживача) складають "суміш.: з двох-трьох фракцій. Якщо немає достатніх гірських масивів, щоб організувати; видобуток щебеню, можна виробляти його подрібненням крупного гравію на щебінь. У цьому разі виключаються затрати на ведення буровибухових робіт. Гравій (щебінь) просіюють крізь набір сит, розміри отворів яких послідовно 1,25Dнб, Dнб, 0,5 (Dнб+ Dнм), Dнм (індекс нб означає найбільший діаметр, нм —найменший), і визначають часткові й повні залишки на кожному ситі, виражаючи їх у процентах за масою до просіюваної проби. Маса проби становить 5, 10, 20,30, 50 кг при найбільшій крупності 10, 20, 40, 70 мм. Якщо немає сит з вічками, діаметр яких дорівнює 1,25Dнб і 0,5 (Dнб + Dнм), то користуються ситами стандартного набору, розміри вічок яких найближчі: до потрібних. Виробництво сумішей на основі без цементних в’яжучих ґрунтується на гідротермальному синтезі гідросилікатів кальцію, здійснюваному в автоклаві при підвищених значеннях тиску й температури водяної пари. Тому такі матеріали й вироби дістали назву автоклавних силікатних. Аби підвищити міцність готових виробів, замість вапна застосовують вапняно-піщане в'яжуче, виготовлене одночасним помелом грудкового негашеного вапна та кварцового піску. Змінюючи співвідношення між компонентами в'яжучого та тонкість помелу, регулюють активність в'яжучого та міцність готових виробів. При виготовленні автоклавних силікатних сумішей та виробів можуть використовуватися також в'яжучі, які містять вапно. Їх виготовляють одночасним помелом негашеного вапна та гранульованого шлаку чи активних мінеральних добавок. Можна також використовувати білпозий (нефеліновий) шлам.[18] Технологія виготовлення фарбових сумішей відрізняється в залежності від типу та призначення суміші. Оліфи — зв'язуючі для олійних фарбових сумішей, це продукти нагрівання до 160... 300 °С (варіння) рослинних висихаючих олій (лляної, конопляної, тунгової) при безперервному перемішуванні й продуванні крізь них повітря. Щоб прискорити висихання оліфи, під час .варіння олій до них додають 2...4 % сикативів — солей оксидів свинцю, марганцю, кобальту чи розчини інших металевих солей жирних кислоту органічних розчинниках. Таким чином, при виготовленні натуральної оліфи відбувається процес полімеризації вихідного мономеру. Внаслідок тривалого нагрівання при температурі майже 300 °С чи при продуванні гарячого повітря (оксидації) молекули олії з'єднуються одна з одною в місцях подвійних зв'язків, які існують у жирних кислот, тобто полімеризуються, утворюючи макромолекулу полімеру — оліфи. Плівка, утворена після висихання оліфи, містить 100 % олії і має підвищену водостійкість, еластичність, глянцевитість та атмосферостійкість. Напівнатуральні, або ущільнені оліфи — виготовляються за допомогою варіння (при температурі полімеризації 300 °С) деяких напіввисихаючих та невисихаючих рослинних олій — соняшникової, соєвої чи бавовняної. Ущільнення олій при виготовленні таких оліф досягається окислювальною полімеризацією за допомогою продування крізь шар олії повітря, нагрітого до 150 °С. Одержані в'язкі полімеризовані олії розбавляють до рідкої консистенції органічними розчинниками. Класифікація асортименту будівельних сумішей Номенклатура будівельних сумішей надзвичайно різноманітна, проте вони органічно взаємоповязані спільним функціональним призначенням – використанням у будівництві. Основним критерієм для зіставлення різних видів матеріалів є їхні технічні властивості. Суміші на основі цементних в’яжучих. Сюди відносять в першу чергу бетонні суміші. За основним призначенням бетонні суміші поділяють на конструкційні і спеціальні (жаро- та хімічно стійкі, декоративні, радіаційно-захисні, теплоізоляційні тощо); за видом заповнювачів — на щільних, пористих і спеціальних заповнювачах; за структурою — щільні, поризовані, ніздрюваті, крупно-пористі. Крім того, бетони класифікують за середньою густиною: особливо важкий середньою густиною понад 2500- кг/м3. Такий бетон на заповнювачах із звичайних щільних гірських порід одержати не вдається, тому використовують барит, залізні руди, сталеві ошурки, стружки; Важкий (звичайний) середньою густиною 2200...2500, кг/м3 на заповнювачах із щільних гірських порід (щебінь, гравій, пісок). Це найпоширеніший різновид бетону; полегшений середньою густиною 2000...2200 кг/м3 на заповнювачах зниженої щільності (вапняк-черепашник, цегельний бій); легкий середньою густиною 500...2000 кг/м3 на природних і штучних пористих заповнювачах (вулканічні та вапнякві туфи, пемза, керамзит, шлакова пемза, аглопорит); особливо легкий середньою густиною до 500 кг/м3; це насамперед. : ніздрюваті бетони та бетони на особливо легких заповнювачах (спучені перліт і вермикуліт). Розрізняють також бетонні суміші за розмірами крупного заповнювача. Верхня границя крупності заповнювача лімітується перерізом елемента виробу чи конструкції, розміщенням та ступенем насичення арматурою, відстанями між її прутками. [19] За розмірами заповнювача розрізняють бетонні суміші: крупнозернисті — із заповнювачем найбільшою крупністю від 10 до 150 мм; дрібнозернисті — із заповнювачем найбільшою крупністю до 10 мм. За показниками легкоукладності бетонні суміші поділяють на марки, наведені в табл. 1. Марка за легкоукладністю | Норма легкоукладності за показнлком | Марка за легкоукладиістю | Норма легкоукладальності : за показником | жорсткості, с | рухливості, см | жорсткості, с | рухливості, см | Ж 4 Ж 3 Ж 2 Ж 1 | 31 і більше 21...30 11...20 5...10 | - - - - | П1 П2 ПЗ П4 | 1...4 - - - | 4 і менше 5...9 10...15 16 і більше |
|